Register for Cleanetechnics Weekly substance for Zach and Scotts Detailed analyzes and summaries on a high level, register for our daily newsletter and/or follow us in Google News!
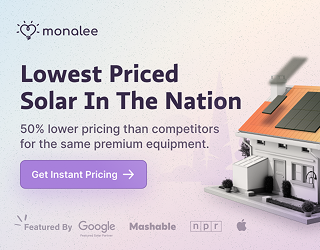
Last updated to: April 25, 2025, 6:12 p.m.
At a dusty solar location outside of Culcairn, New South Wales, a persecuted robot was methodically rolled between rows of steel posts, which raises large photovoltaic panels with a vacuum arm and placed them on prepared fastening structures. This string machine did not stop in the brutal Australian sun, in which manual workers need regular moisture widths and safety protocols for heat stream. It marked a quiet turning point in the history of the sunrise. The robot created in Shanghai based in Shanghai was not an experiment. It was a production unit that did production work. And it was just replacing the output of a crew of three or four installers at one of the largest projects in the country's user workshops.
The global solar industry has a speed problem. It is not the case that we do not know how to build solar systems, since gigawatts are added with new capacity every year. The problem is that the scale and the speed are necessary that have reached the climate goals that have to train and use our ability to find, train and use human muscles to physically install everything. According to IEA, the world must install over 800 gigawatt solar annually in early 2030 in order to stay up to date for net-zero. That means hundreds of millions of modules every year. Moving a 30-kilogram glass rights from a palette, the pile of heaters, which precisely aligned with a torque tube and for weeks again in the heat, is not only time-consuming. It is physically punished. Local shortages, injuries and burnout all limit the throughput. Automation is not just a convenience, but becomes a necessity. This is far from the early days of sunlight when road collection for unskilled day work was the norm.
Springing's robot system, which is used commercially for the first time in Culcairn, is a persecuted vehicle with a robot arm with six axes, which is equipped with an AI-controlled vacuum suction gripper. It uses 3D sensors, attitude recognition algorithms and slam navigation (simultaneous location and mapping) to position yourself at the millimeter level within the precision. As soon as it is loaded with a stack of panels, it moves autonomously through the array, identifies the assembly points, aligns each module and places it. According to the field data from the project, the robot panels installed 480 on a standard-hour day at a speed of around 60 per hour. This is about three to five times faster than a typical human crew of four people who often occur at around 100 to 1220 modules per day due to tiredness, heat limits and the need for team coordination.
This is part of a wider industrial trend. In the United States, Rosendin Electric demonstrated its own half-autonomic system in Texas, which made it possible for a two-person team to install 350 to 400 modules a day, a clear level compared to traditional methods. The AES Corporation has developed a robot called Maximo that combined placement and fastening with computer vision. Trina Solars Trinabot in China works in a similar space, with prototype systems over 50 modules showing per hour. The selection of the architectures varies – some systems are completely autonomous as that of submissions. In an industry in which time-to-energy is critical, the shaving weeks according to the construction plan reduces the costs directly and increases net sales.
What distinguishes the system from Springing is full autonomy. As soon as it is staged and calibrated, it deals with navigation, avoidance obstacle and precision plan. This is a large award of power-assist systems that are still strongly based on human inputs. Of course, this autonomy has its own restrictions. The robot needs a relatively well trained area and distance that offers its 2.8-meter chassis. Places with steep slopes, heavy mud or dense rock slow down or stop it. And while his AI can adapt to changes in light, intensive glare or poor visibility can affect the sensor performance. It may also be necessary for a person to follow the final mechanical fastening depending on the racking system used. In this sense, the robot of jumping still depends on the design standardization in user transactions – the flatter of the website and the easier the racking, the better it is carried out.
There is also the question of logistics. A robot cannot magically summon his own panels. A constant feed from modules is needed at a short distance from its work area. This means that forklifts or telepaters have to be synchronized with the movement of the robot to prevent downtimes. This is not a major hurdle in projects in which layout planning and material river are already permanently managed, but it requires a shift in the attempt to think. Baumanagers now have to plan the robot logistics as they are planning crane movements or concrete enjoyment. And while the robot does not need breaks, the charge must be charged. One jump has not published detailed specifications, but the drive train seems to be electrical, probably with an LFP battery system that can be exchanged or recharged overnight. The perseverance for a complete shift can be reached, but the double shift company would require a charging infrastructure.
From a financial point of view, the business case is convincing. Workers make up a significant part of the engineering, procurement and construction costs for solar on the scale of care. If a robot can reliably replace three to four employees and do this with fewer errors and injuries, the repayment time is short – especially if the machine is rented or reused over several projects. The savings of the introduction of information installation costs in the range of 30%, although the real figures depend on details and how well the robot is integrated into the workflow. A case study from the Culcairn use showed that the overall project schedule was reduced by around 25%, which was partly reduced thanks to the consistent throughput even in high heating periods, in which human workers were usually slower.
The promise of autonomous robot outdoor workers are demonstrated in Australia, but it will be essential in many places around the world, since the temperatures of the wet light bulb make it impossible for human work to work. Think of construction, agriculture, street work. During the installation of the Culcairn Solar Farm in New South Wales ,, The area had a peak time temperatures of 36.2 ° C (97.2 ° f) on January 11th, with several more days being above 34 ° C . We move into a world in which the work on the equator on summer day will often be impossible. The scorching and dry Australian summer outback is part of the future more countries.
There are other implications here. If the sun furnishings are similar to a factory floor – very repeatable, automated and scalable – the way we think about the energy infrastructure changes. A future in which fleets of machines act with the assembly of the panel, perform O&M drones thermal scans and autonomous brush bots are no longer speculative. It's just intelligent engineering. Solar is more like the production: controlled, modular and fast. This in turn makes it easier to finance, use and wait. And it means that the workforce also develops – not from humans, but to people who supervise, remove and orchestrate the robots.
The robot of one jump is still early. It was only used commercially in a handful of places: Culcairn in Australia, parts of Adanis 30 GW Khavda Park in India, and tested in China's high-wonders and desert solar zones. But the direction is clear. The future of sunrise will be faster, safer and more precise – not because of human muscles, but because of the repetition of robots. There will still be people on site, but their role shifts from lifting plates to manage throughput. Just as cranes and excavators have changed civilian construction, robots such as the next era of solar use will also be defined.
Regardless of whether you have solar energy or not, please carry out our latest solar power survey.
https://www.youtube.com/watch?v=2Bon_R1cveo
Do you have a tip for CleanTechnica? Do you want to advertise? Would you like to propose a guest for our Cleanetech Talk Podcast? Contact us here.
Register for our daily newsletter for 15 new Cleanetech stories per day. Or register for our weekly top stories of the week if the daily daily is too common.
CleanTechnica uses affiliate links. See our politics here.
CleanTechnic's comment policy