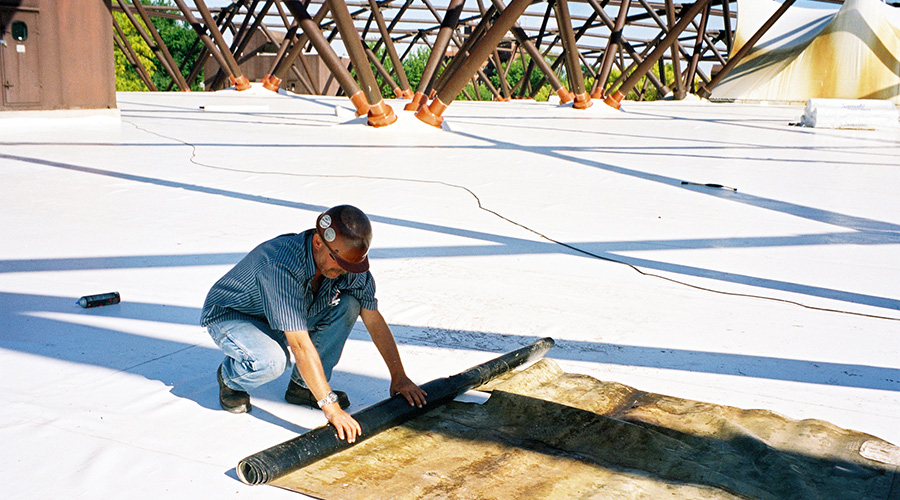
The move of the roof industry of vinyl (PVC) to increase recycling to the consumer.
The vinyl (PVC) roof membrane industry has done an excellent job to minimize waste in its own manufacturing processes. An estimated 99.5 percent of the production waste are collected and recycled into new roof products. This so -called recycling in front of the consumer, which was carried out by manufacturers in front of a product, leads to half a percent of raw material waste. Despite such a seemingly positive sustainability status, the industry takes even more steps to further reduce it via its way to the Zero program.
When it comes to recycling PVC roofs according to the consumer, the industry is working hard to sharpen awareness with its end users and other stakeholders in institutional and commercial institutions. In order to be successful, recycling according to the consumer requires the participation of construction owners, facility managers and contractors to promote the efforts. By deciding to make a more sustainable decision, the collective buy-in these decision-makers can help to simply thrown them into a dumpster and sent to the landfill. Instead, they can be recycled for use in other applications, including new umbrella support materials.
The PVC roofer industry is pleased that since the start of the recycling efforts in 2014, 200 million pounds before and after the consumer PVC roof bonds have avoided the landfill. In 2024 alone, 10 million square foot were recycled according to the consumer roof area. However, there is still a lot to do.
Overcome resistance
Many building stakeholders still speak of reserved PVC fighting. Sometimes it is because you do not know the right procedure for collecting old roof membrane. You could also fear the unaffordable expenses. The vinyl roof development of the Chemical Fabrics and Film Association (CFFA), the professional advocacy representative of the PVC roofer industry, tries to demry the recycling process and increase the number of residing projects that begin with recycling the original PVC roof.
The vinyl roof division has turned to two experts from the roof and PVC industry in order to form the reaction to a stronger participation in recycling efforts. Brian Whelan is the owner of Roof Resources and Past Executive by Sika Sarnafil. Richard Krock is the owner of Vychlor Advisors, LLC and former Senior Vice President of the Vinyl Institute. These most important advisors both have more than three decades in the roof and PVC industry and are pioneers in terms of the recycluability of roofers and the initiatives for green buildings.
“As an organization, we try to raise awareness of the effectiveness of the PVC roofing membrane recycling,” says Whelan. “There is a great variety of consciousness. Some construction owners do not recognize that recycling is even possible that they can prevent an old roof on a landfill.
The association tries to answer some of these questions. It has recently released an animated video that covers the PVC roofrecycling process, from the first meeting to the final flat bed that goes to the recycling system.
https://www.youtube.com/watch?v=3SORIN-5JG
New video explains lightness
The video makes it clear that only a few additional steps and minimal additional work are required to remove mechanically fastened or shared PVC roof membranes and to pack them for recycling.
The recycling of PVC roof membrane receives the resources and minimizes the building materials disposal of landfill. The first step in a successful roof recycling project is to carry out a kick -off meeting with all stakeholders in order to discuss recycling steps, logistics, storage and treatment of the existing PVC membrane.
Often, the papers that form the core of new PVC membrane rolls can be reused to roll the existing PVC membrane. Next, roofers have to cut the existing PVC membrane into manageable pieces.
Building stakeholders will also be happy to find out that there is no real way to pack and bundle the old roof on pallets. The video explains several popular options such as the pyramid configuration, the candy sweetness method, the log house method and the cutting and stacking method. The most important thing is that the membrane is packed in such a way that it is safe to stop off the roof and transport it into recyclers with fully loaded flat bed vehicles. The maximization of the old roof volume, which is the truck, lowers the recycling costs and also affects the benefits of CO2 footprint.
Recycing the advantages
In addition to the new video, the vinyl roof department submitted a paper at the National Institute for Standards and Testing (Nist), which quantified the first of its kind that quantified the carbon advantage of recycling PVC roof construction. The paper was first presented at the Remade Institute in 2025 in Washington DC, which is financed by the US Ministry. A publication date is imminent.
“With the paper we would like to give the owners something more tangible that they can pay attention to and say:” That is why we decide to recycle, “says Krock, who finds that the US environmental protection authority has reached a recycled quota for all land for the whole country by 2030.
The recycling of a roof is aimed at certain green building certification. If the building is already certified, the project can qualify as part of maintaining the certification.
“Even without certifications, recycling of a roof can be reported as a sustainability initiative under disclosure on environmental, social and governance (ESG),” says Krock. “The international sustainability standards board includes the ESG guidelines for financial reports.”
Recycled PVC roof bonds can contribute to processes with closed loops and open loop processes. In a closed loop process, PVC roof movement is recycled and used to produce new PVC roof membranes, roof paths and accessories. In an open loop process, PVC roof movement is recycled and used to manufacture other products as roof production. These products often include floor coverings, concrete extension and other products. Both closed and open loop methods avoid deposit and contribute to the reduction in carbon.
Add the costs
Of course, as in every shop, the costs are a problem. Whhelan and Krock admit that every job will be different, and it is difficult to give the building owners a rule of thumb how much they can expect if they add recycling to their reversing projects.
“The reality is, you won't know until you spend the job,” says Krock. “We recommend that project owners have an advertising book shape in their bid form and ask the roofers to enter the costs associated with a potential recycling of the old roof. In this way, fazility managers can clearly recognize how much additional it will cost, and whether they believe that the effort is worthwhile.”
Obviously, the PVC roofer industry believes that it is absolutely worth it.
“It is a value to recycle a roof,” says Whelan. “Of course it's right. From the perspective of sustainability, there is no better way to be a good community partner.”
Bill Bellico is a marketing chairman of the Chemical Fabrics and Film Association (CFFA), an international trade association that represents manufacturers of polymer base and film products. They are involved in the construction and construction industry, but are not directly manufactured.
Related topics: