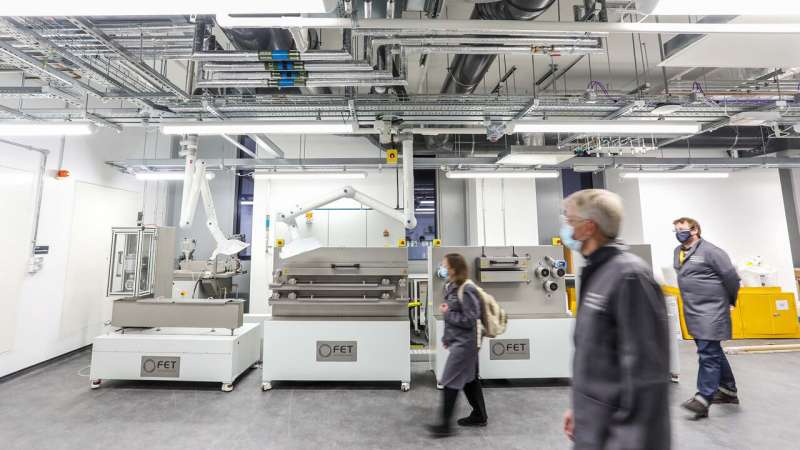
Lignin case study laboratory. Credit: Manchester University
Carbon fiber is a critical material for industries such as aerospace and automobile, which are valued for their strength and easy properties. However, conventional carbon fiber production is based on costly petroleum -based materials that increase costs and environmental effects.
Lignin-a-widespread by-product of cellulose production with around 70 million tons annually produced a promising, sustainable alternative. Lignin is typically treated as a waste or energy and has undeveloped potential for high -quality applications, including the next generation carbon fiber production.
From the laboratory to Pilotkala
The industrial partner Lixea had previously worked with Imperial College London, where researchers developed a patented technology to convert lignin into carbon fiber in a small laboratory scale (1 ml production). The process used two important innovations:
- Ionic fluid technology – various lignins, while the liquid can be recycled after the fiber is formed.
- Polyvinyl alcohol (PVA)-a non-toxic, biodegradable polymer that is used as a spinning aid.
This approach not only enables the production of Hochlignin-in-in-in-Kon-Incontent fibers (75%–90%) with excellent structure and yield, but also significantly reduces the costs. The replacement of precursors based on petroleum and ionic fluids-sowing is reduced renewable, lower costs and less toxic material-acceptable product costs by three to five times.
Manchester's ability to scale
In order to validate this technology on a scale, researchers at the University of Manchester, under the direction of Jonny Blaker, professor of biomaterials, have created a demonstration in the pilot level on the FIBRE Technology platform at the Henry Royce Institute using his WET spinning line. Lignin was from the Lixea pilot plant that uses the same ionic liquid to extract lignin from wood waste to ensure the process orientation with the company's existing technologies.
The Manchester team tested three different lignine two from the sawdust of Spruce, and one of Bagasse, a by-product of the sugar production with the lignin derived from Bagasse, which enables itself most effectively as effective and the first time continuous fibers on the pilot scale .
Key learning and future development
Several critical knowledge came from the exams. First, drying control was of crucial importance to prevent the shrinkage of fibers. Second, Lignin solutions became viscoser over time and required adjustments to maintain the quality. And thirdly, the spin -off design influenced the uniformity of the fiber and underlined the need for further refinement.
Thanks to the project, the team successfully produced continuous fibers up to 5 meters long. The next steps are the refinement of fiber drying, collective and carbonization processes, which will be essential for the scaling of this breakthrough technology in Great Britain
A milestone for sustainable carbon fiber
Manchester's success in scaling this new technology is an important step towards a commercially sustainable, sustainable carbon fiber production.
“We are pleased to use our ability to show the scaling potential of this pioneering process in order to create an inexpensive, renewable alternative to conventional production.
“Thanks to the equipment and specialist knowledge that are available in our pilot facility, we were able to produce continuous fibers with Lignin from Lixea, which deal with the most important challenges in formulation and fiber drying and at the same time ensure that it could work with the wood fractional technology from Lixea .
“This attempt is a considerable step to make inexpensive, renewable carbon fiber reality,” says Professor Blaker.
With continued advances and cooperation in the industry, carbon fiber in Lignin could soon become a commercially scalable, powerful and environmentally friendly alternative to metroleum derived. Manchester's pioneering role in technological scale-up increases its position as a leader in material innovation and sustainable production.
Provided by the University of Manchester
Quote: Scaling of sustainable carbon fiber production: A breakthrough in the lignin-based technology (2025, February 17) accessed on February 17, 2025 by https://phys.org/news/2025-02-Scaling-sustable- carbon-production.htmlml
This document is subject to copyright. Apart from a fair handling of the purpose of the private study or research, no part may be reproduced without a written approval. The content is only provided for information purposes.